Rubber product development
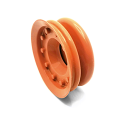
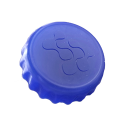
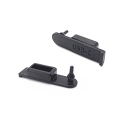
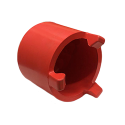
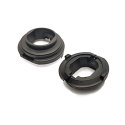
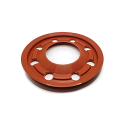
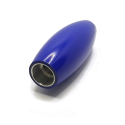
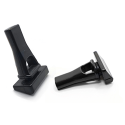
How does the product development
of rubber mouldings work exactly?
1
Concept phase
Consulting
You, either the final consumer or a manufacturing company, gets in contact with us for Rubber Product Development to explain your needs, quantities, features and to request a price. Basically, the final product will be introduced, sometimes totally defined sometimes only as an idea/concept. At this stage, the Waldeks Team will carefully understand every aspect of the project and get ready to prepare an offer.
In order to fully support our clients, every data format is welcome: 2D drawings, 3D model, reverse engineering, verbal explanation, etc. Once we have everything, we will promptly work on a suitable offer for your budget
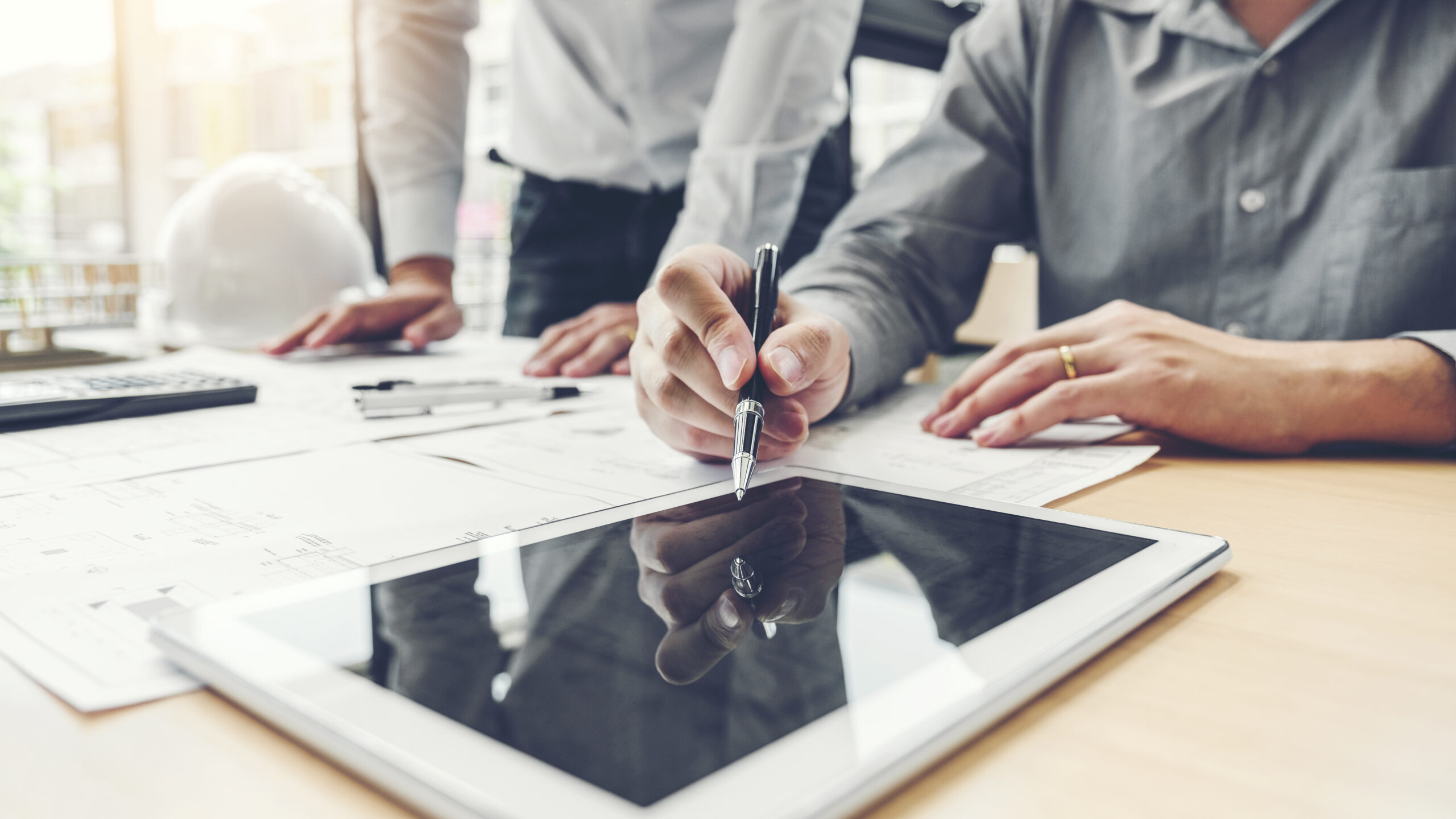


2
Designing
Valididation from client
Once the first phase is cleared, we move to the Rubber Product Development and Injection Mold Engineering. Here the final geometry of the part and the production requirements will be defined. Some features get validated and agreed between both parts:
- rounding edges;
- surface finishing;
- part’s nesting / positioning;
- rubber shrinkage and other details.
Manufacturing conditions are also considered at this stage. Some
important points are:
- parts per mold;
- molding type (injection / pressing)
- machine model (tool boundaries)
- tool material (Aluminium, Steel, Hardened Steel, 3D Printed)

3
Analysis & Optimization
required for complexe parts
Not every idea comes ready! Most Rubber Product Development and new concepts may have opportunities for optimization. The improvements can be over functional parameters or manufacturability, which correlates to the price. With a strong background on both tooling and manufacturing of rubber components, we verify possible misconceptions and future failures through a Design Validation Process. Additionally we support our clients on modifications or required analysis. Using the most up-to-date engineering software we analyze both the part and the molding tool for:
- stress concentrations (structural analysis)
- Air flow / bubble formation
- Injection points and homogeneous rubber distribution.
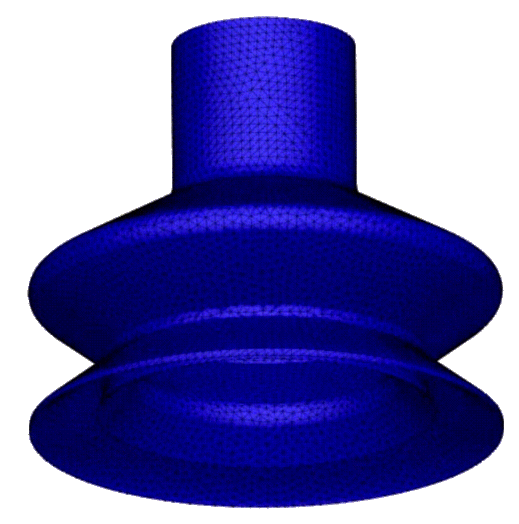

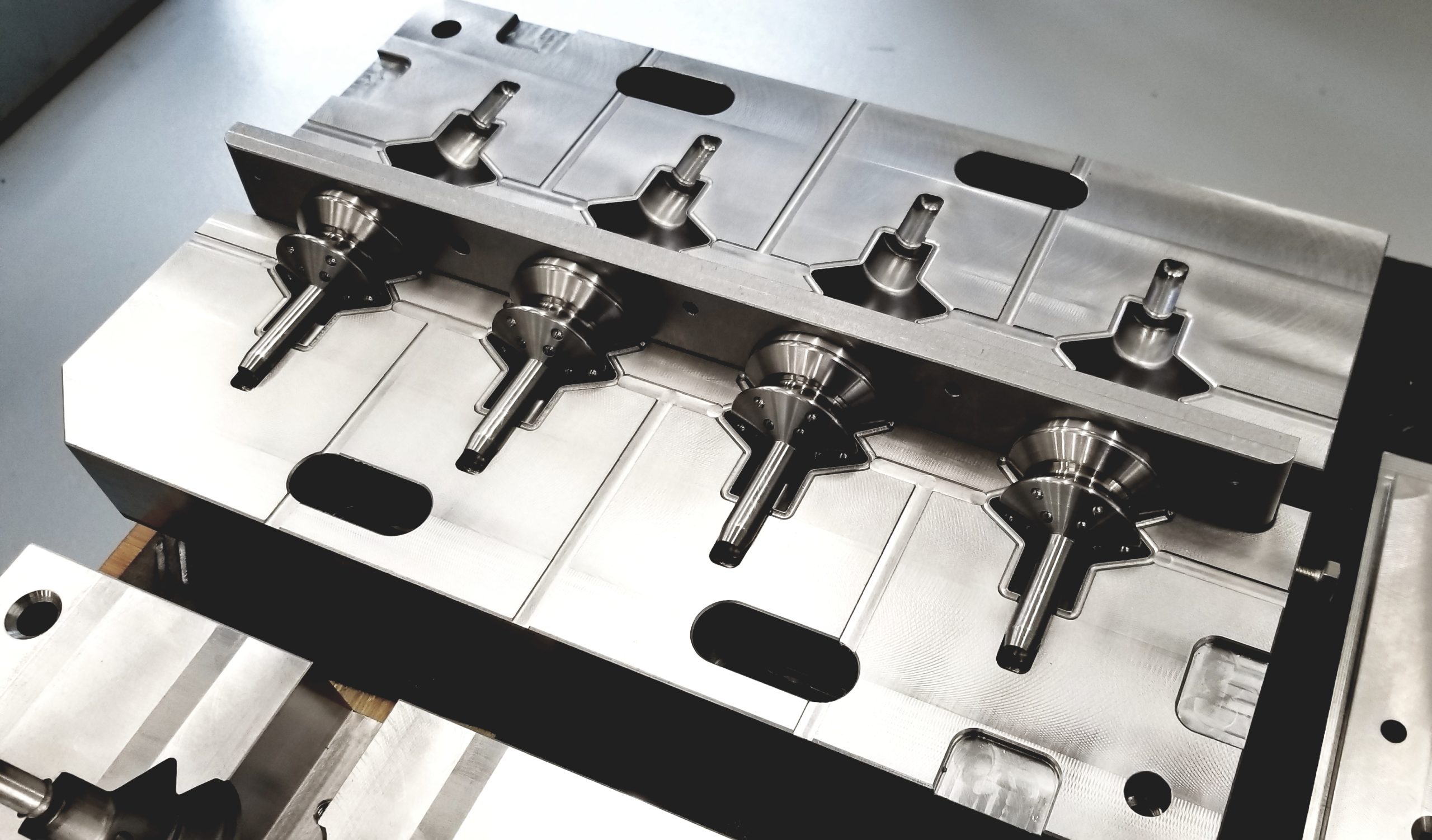
4
Tool manufacturing
machining or 3D printing
Possible by our modern production center, it is time to transform the design into reality. Several processes are necessary to produce a high-quality tool which will delivery precise and uniform parts over the time. Not only the part’s geometry is important, but also the wear resistance (life of the tool) and its functionality (working time).
Most of our tools go through a series of process until its completion, some examples are:
- 3 and 5-axis milling
- CNC Turning
- EDM (die sinking)
- Electro polishing
- Sanding / deburring
- Dimensions control (3D measurements)

5
Vulcanization
Self usage / outsourced
Once the mold is ready to be used, it is shipped to the client so they can start the manufacturing. Although our company specifically do not vulcanize or runs any production, we do have a network of extremely professional and reliable rubber manufacturers. Through this intermediate support, we would surely take care of your production and provide your parts on the long run, from end-to-end.
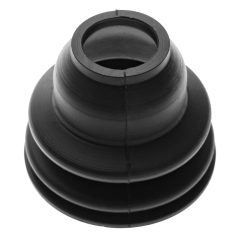